To be added. Contact Janderson(at)nitrofreeze.com to contribute.
Plastic Deflashing Service Provider Directory
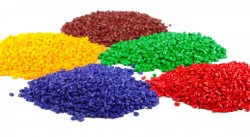
Want to submit a company listing? Register your company here. North American Deflashing Vendors USA- Northeast Cryogenic Deflashing –Nitrofreeze Cryogenic Solutions (Worcester, MA) Thermal Energy Deflashing Blast Deflashing –Precision Finishing Services (Windsor, CT) Magnetic Abrasive Deflashing Ultrasonic Vibration Deflashing –Precision Finishing Services (Windsor, CT) –Cleaning Deburring Finishing, Inc. … Continue reading